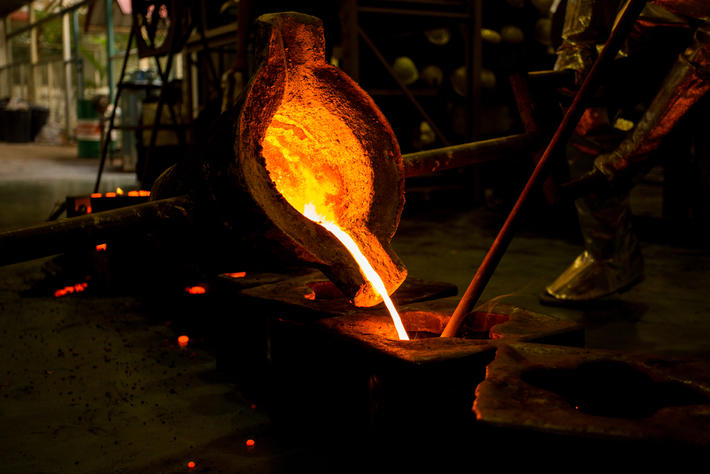
La decarbonizzazione delle fonderie: nuovi obiettivi per la massima sostenibilità ambientale
Nonostante la complicata congiuntura degli ultimi anni, le imprese hanno continuato a investire per ridurre l’impronta ambientale dei propri prodotti, ottenendo importanti risultati.
Superiore al venti percento è la percentuale degli investimenti dedicati all’ambiente dalle imprese del settore sul totale degli investimenti lordi in beni materiali: un dato davvero significativo, soprattutto se paragonato ai dati ISTAT relativi sia all’industria considerata nel suo complesso (circa 1,5%), sia alla metallurgia intesa in senso ampio, cioè facendo riferimento al codice Ateco 24, che si colloca in una forbice compresa fra il 3,5 e il 4%.
Numeri di questa portata ben evidenziano come sia ormai chiaro, alle imprese del settore, che intervenire per ridurre gli impatti ambientali che le attività di fonderia potenzialmente comportano sia oggi, al di là delle mere esigenze di compliance alla normativa ambientale, cruciale per potersi garantire un importante vantaggio competitivo.
La crescente sensibilità della società civile e delle pubbliche amministrazioni nei confronti di questi temi e della decarbonizzazione sta infatti portando allo sviluppo di sistemi di valutazione e di certificazione della sostenibilità ambientale che, sempre più spesso, coinvolgono non soltanto i produttori di beni o servizi destinati al consumatore finale, ma anche le imprese che realizzano componenti intermedi nell’ambito delle catene di subfornitura, come è il caso delle fonderie.
Economia circolare: sempre più elevato l’utilizzo di materiali di recupero come materia prima seconda
La fonderia costituisce un elemento centrale del modello economico “circolare”: l’attività di fusione rappresenta infatti, da sempre, la tecnica attraverso la quale è possibile l’utilizzo dei rottami allo scopo di dare vita a nuovi prodotti. Come tale, l’impresa di fonderia rappresenta l’essenza del concetto di circolarità che vede il rifiuto al centro delle attività finalizzate alla sua valorizzazione economica.
Stando ai dati raccolti su un campione di imprese rappresentativo del 37% della produzione totale di getti in Italia, negli ultimi anni si registra un ulteriore leggero incremento nell’utilizzo di materie prime da riciclo.
Le fonderie di metalli non ferrosi, per la carica dei forni, utilizzano soltanto lingotti di alluminio o di altre leghe leggere. Questo non significa, però, che la materia prima utilizzata non sia proveniente dal riciclo: buona parte dei lingotti utilizzati dalle fonderie non ferrose italiane proviene infatti dalla rifusione, da parte dei raffinatori, di rottami non ferrosi provenienti dal riciclo. I prodotti delle fonderie, inoltre, siano essi di metalli ferrosi o di metalli non ferrosi, presentano cicli di vita molto lunghi e, al termine del loro utilizzo, possono a loro volta essere riciclati per dare origine a nuovi prodotti, in un eterno ciclo inesauribile.
Scarti di produzione: meno volumi e più riutilizzo per la decarbonizzazione delle fonderie
Il settore della fonderia, in particolare quella con sistemi di formatura in sabbia, è caratterizzato da un elevato rapporto rifiuti/prodotto netto. L’attenzione delle imprese del settore, negli ultimi anni, si è molto focalizzata sulle modalità di gestione dei residui dei vari processi lavorativi, sia allo scopo di diminuirne le quantità, incentivando i riutilizzi all’interno dei processi di fonderia stessi, sia ricercando possibili riutilizzi esterni alternativi alla tradizionale attività di smaltimento.
Emblematico della tendenza verso l’economia circolare nella gestione dei rifiuti è il caso delle terre esauste. Oltre alla diminuzione in assoluto dei quantitativi prodotti, passati dai circa 575 chilogrammi per tonnellata di getti prodotti del 2000 ai 324 del 2019 (con una riduzione superiore al 43%), è interessante osservare come attualmente oltre il 95% delle terre esauste venga recuperato attraverso riutilizzi esterni in impieghi come materie prime in sostituzione di sabbie e terre da estrazione, annullando praticamente il ricorso allo smaltimento in discarica.
Questa tendenza si colloca in pieno accordo, ancora una volta, con i principi dell’economia circolare, che intende valorizzare i residui di produzione (rifiuti o sottoprodotti) quali “materie prime seconde” utilizzabili all’interno di processi industriali quali i cementifici, le fornaci, o ancora per la fabbricazione di manufatti per l’edilizia e l’ingegneria civile.
Proprio per incentivare ulteriormente questa tendenza, è stato istituito il Tavolo Tecnico “Scorie di fusione”da Regione Lombardia. L’obiettivo di questa iniziativa è quello di fornire a tutti i soggetti coinvolti un quadro di riferimento tecnico-normativo chiaro e condiviso per la gestione circolare di alcuni dei principali residui delle attività siderurgiche e metallurgiche presenti sul territorio regionale.
Emissioni climalteranti: verso la carbon neutrality
Secondo lo studio “Strategia per la decarbonizzazione dei settori Hard to Abate”, redatto da Interconnector Energy Italia e dalle associazioni confindustriali, in collaborazione con Boston Consulting Group, i sette settori industriali più energivori (acciaio, cemento, carta, ceramica, chimica, vetro e fonderie) producono complessivamente circa il 20% delle emissioni dirette di gas serra in Italia.
Anche se solo una minima parte di queste emissioni è riconducibile alle fonderie, le imprese del settore sono da tempo impegnate nella riduzione delle loro emissioni di gas climalteranti e, nei prossimi anni, saranno chiamate ad affrontare un ulteriore e impegnativo cammino, in termini tecnici e di impegni economici, verso gli obiettivi di decarbonizzazione fissati dall’Europa Proprio per tracciare una roadmap delle azioni necessarie a raggiungere la neutralità carbonica entro il 2050.
È stato infatti siglato l’Industrial DecarbonizationPact, un’alleanza per la decarbonizzazione dell’industria che ha l’obiettivo di assicurare una transizione ecologica rapida e inclusiva, in grado non solo di raggiungere gli obiettivi indicati da Bruxelles ma anche di preservare la competitività sui mercati internazionali di settori che rappresentano la spina dorsale dell’economia italiana.
Dal punto di vista tecnico, nell’ambito del settore delle fonderie il principale strumento al quale far riferimento per realizzare gli obiettivi di decarbonizzazione richiesti è l’elettrificazione delle imprese. La seconda leva in ordine di impatto potenziale riguarda l’utilizzo di biocombustibili nei forni a gas.
Secondo quanto stimato dallo studio realizzato da Boston Consulting Group, già al 2030 la completa elettrificazione dei forni a cubilotto, l’elettrificazione parziale (circa il 20%) dei forni a gas e l’utilizzo di biocombustibili nel restante 80% dei forni a gas permetterebbe una riduzione delle emissioni dirette di CO2 pari a circa il 50%. La completa elettrificazione dei restanti forni a gas, in orizzonte 2050, porterebbe ad abbattere del 90% le emissioni dirette generate a oggi dalle imprese del settore.
La sostituzione dell’attuale parco forni che opera utilizzando vettori energetici quali coke e metano con forni elettrici richiederà non solo uno sforzo economico importante, che dovrà necessariamente essere supportato da appositi strumenti finanziari e/o fiscali, ma necessiterà anche di interventi per rendere disponibile la quantità di energia elettrica necessaria; al riguardo, lo studio stima che al 2030 il fabbisogno di energia elettrica dei settori hard to abate sarà di 64 TWh, di cui circa il 40% “verde”.
Perché il processo di elettrificazione sia sostenibile, inoltre, saranno necessari importanti interventi normativi finalizzati a rendere competitivo il prezzo dell’energia elettrica che attualmente, nel nostro Paese, registra un importante divario di prezzo rispetto ai partner europei, anche a causa di differenti regimi gestionali degli oneri legati, ad esempio, ai costi indiretti dell’energia.
Emissioni di polveri: drasticamente ridotte grazie alle nuove tecnologie
Un altro aspetto su cui le imprese del settore hanno costantemente lavorato negli ultimi anni è quello relativo alle emissioni di polveri: le fonderie, in particolare quelle che utilizzano processi di formatura in sabbia “a perdere”, ne originano in tutte le fasi del processo produttivo, dalla fusione alla finitura dei getti. Anche la produzione di getti di metalli non ferrosi in forma permanente origina emissioni di particolato, quantificate in termini di “nebbie oleose”.
Il ricorso alle tecniche BAT (Best AvailableTechniques) e gli sviluppi delle tecnologie end of pipe hanno consentito il raggiungimento di importanti obiettivi di riduzione delle emissioni residue. Questa tendenza si è registrata anche nel periodo 2017-2019 con un -12,5% medio rispetto al 2015. Il dato è ancor più significativo se si considera che il livello di emissioni del 2015 era a sua volta inferiore del -65% rispetto a quello del 2003.
Energia: sempre più numerosi gli interventi di efficientamento
Il tema dei consumi energetici per un settore “energy intensive” costituisce non soltanto un aspetto ambientale rilevante, in particolare in relazione al tema della decarbonizzazione delle fonderie, ma anche uno dei principali fattori di costo del getto.
Per tutte le tipologie di fonderia sono le attività di fusione ad assorbire la quota di energia prevalente: queste incidono per il 63% nelle fonderie di ghisa, per il 54% in quelle di acciaio e per il 35% nelle fonderie di alluminio. È dunque in questa fase del processo che si possono collocare gli interventi di efficientamento più significativi, come risulta del resto dall’analisi dei dati contenuti nella “Linea Guida per la redazione delle diagnosi energetiche nel settore delle fonderie”, realizzata da Enea in collaborazione con Assofond.
La Linea Guida contribuisce a diffondere nel settore la consapevolezza dell’importanza dell’efficientamento energetico, fornisce alle imprese un contributo concreto e fa parte della collana “Quaderni dell’Efficienza Energetica”. Si tratta di una guida operativa sia per le imprese operanti nel settore delle fonderie sia per i professionisti coinvolti nella redazione di una diagnosi energetica di “qualità” e conforme all’Allegato II del D.lgs. 102/2014.
La pubblicazione riporta le principali voci di consumo energetico dei siti produttivi, le indicazioni per la messa in opera di un sistema di monitoraggio adeguato al settore, gli indici di prestazione energetica relativi sia all’intero impianto che ad alcuni processi e, infine, un’ampia panoramica dei possibili interventi di efficientamento energetico presenti nella letteratura scientifica e tecnica, congiuntamente a una valutazione sia economica che energetica degli interventi effettuati e proposti riportati negli scorsi anni nelle diagnosi energetiche pervenute a Enea.
Proprio le analisi effettuate sulle diagnosi hanno consentito di quantificare i risparmi energetici individuati e realizzati dalle imprese del settore a seguito delle diagnosi energetiche effettuate. Si tratta di risparmi importanti che, per quanto attiene i consumi di energia elettrica risparmiabili, ammontano complessivamente a 86.800 MWh, corrispondenti al consumo annuale di 32.134 famiglie tipo. I 370 interventi effettivamente realizzati, invece, hanno permesso alle imprese del settore di risparmiare complessivamente circa 2.800 TEP (Tonnellate Equivalenti di Petrolio) all’anno.
Fonte: In Fonderia – ll magazine dell’industria fusoria italiana