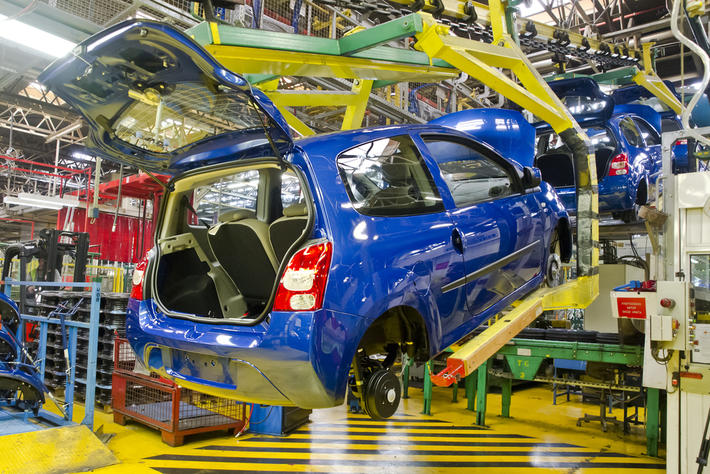
Leghe di alluminio autoinvecchianti per applicazioni nel settore automobilistico
Le leghe di alluminio utilizzate nel settore automobilistico sono trattabili termicamente, poiché tramite tale trattamento è possibile aumentarne considerevolmente la resistenza meccanica. Al fine di ridurre i costi di produzione, recentemente sono state sviluppate leghe di Alluminio innovative, tra cui risultano molto interessanti le leghe di Al autoinvecchianti. Si tratta di leghe di Al-Zn-Si-Mg della serie 7xxx, la cui caratteristica più importante risiede nelle possibilità di raggiungere una buona resistenza meccanica, senza che sia necessario sottoporle ad un trattamento termico. Questo perché sono soggette ad un fenomeno di invecchiamento naturale, a seguito di un periodo di mantenimento a temperatura ambiente, compreso tra i sette e i dieci giorni, raggiungono buone proprietà meccaniche. Utilizzare queste leghe d’alluminio nel settore automobilistico consentirebbe, grazie alla possibilità di eliminare il trattamento termico, di ottenere importanti vantaggi sia da un punto di vista economico sia da un punto di vista di impatto ambientale. Nel presente lavoro di ricerca sono state studiate la microstruttura, la resistenza alla corrosione e le proprietà meccaniche della lega di Alluminio autoinvecchiante (Al-Zn10-Si8-MG EN-AC-7100).
Introduzione alle leghe d’alluminio nel settore dell’automotive
Le leghe di alluminio nel settore dell’automotive sono attualmente ampiamente utilizzate per realizzare componenti meccanici per via delle loro ottime proprietà: bassa densità, elevata resistenza specifica, buona contabilità e buona resistenza alla corrosione. L’utilizzo delle leghe d’alluminio nel settore automobilistico consente di ottenere una rilevante riduzione di peso dei veicoli, con una conseguente diminuzione sia del consumo di carburante sia delle emissioni di gas, riducendo così l’impatto ambientale. Esistono due categorie di leghe di alluminio: leghe non trattabili termicamente, che raggiungono ottimi valori di resistenza meccanica, a seguito di processi di deformazione plastica, eseguiti sia a freddo che a caldo; e leghe trattabili termicamente le quali presentano elevate proprietà meccaniche a seguito dell’applicazione di un trattamento termico. Il meccanismo di rafforzamento delle leghe di alluminio trattabili termicamente è rappresentato dalla precipitazione di precipitati di rafforzamento, i quali si formano durante la fase di invecchiamento che può essere naturale, se condotto a temperatura ambiente oppure artificiale se condotto a temperatura elevata. I primi precipitati che si formano sono coerenti con la matrice di alluminio, ossia presentano lo stesso reticolo cristallino e rappresentano un ostacolo al movimento delle dislocazioni, responsabile della deformazione plastica. Aumentando il tempo di invecchiamento i precipitati divengono incoerenti rispetto alla matrice e costituiscono di conseguenza una fase separata, il che determina una riduzione delle proprietà meccaniche. Durante la fase dell’invecchiamento i materiali possono essere scaldati a differenti temperature e per tempi diversi, il che induce differenti caratteristiche microstrutturali quindi differenti proprietà meccaniche. Attualmente varie ricerche sono state condotte per sviluppare sia metodi di produzione innovativi sia leghe di alluminio per il settore automobilisticocon composizione chimica ottimizzata. Tra queste leghe risultano particolarmente interessanti le leghe di Alluminio autoinvecchianti, ossia leghe Al-Zn-Si-Mg della serie 7xxx, la cui caratteristica principale risiede nell’essere soggette ad invecchiamento naturale, se mantenute a temperatura ambiente per un periodo di tempo compreso tra i 7 e i 10 giorni, a seguito del quale raggiungono buone proprietà meccaniche, senza la necessità di essere sottoposte ad un trattamento termico. La possibilità di eliminare il trattamento termico, grazie all’utilizzo di queste leghe in alluminio nel settore automotive per la produzione di componenti meccanici, consentirebbe all’industria di ottenere importanti vantaggi sia da un punto di vista economico sia da un punto di vista di impatto ambientale. La prima parte del presente studio rappresenta una review del lavoro di ricerca svolto fino ad ora dagli autori di questa ricerca, riguardante la caratterizzazione microstrutturale delle leghe autoinvecchianti in oggetto, mentre nella seconda parte sono riportati i risultati relativi allo studio della resistenza alla corrosione intergranulare e delle proprietà meccaniche di queste leghe.
I materiali e i metodi per l’utilizzo delle leghe d’alluminio nel settore automobilistico
È stato valutato l’effetto sia del contenuto di Mg (wt%) sia di differenti velocità di raffreddamento sulla microstruttura, sulle proprietà meccaniche e sulla resistenza alla corrosione intergranulare della lega EN-AC-7110 (AlZn10Si8Mg). In condizioni di equilibrio la massima solubilità del magnesio nell’alluminio è pari a 17.4 wt%, generalmente il contenuto di MG non supera il 5% nelle leghe di Al da deformazione plastica, mentre per quanto riguarda le leghe di Al da fonderia non supera il 10%.
Nel presente lavoro di ricerca sono state realizzate tre differenti leghe, indicate come AlZn10Si8Mg, AlZn10Si8Mg1 AlZn-10Si8Mg3.
I campioni utilizzati per l’analisi microstrutturale, le prove meccaniche e le prove di resistenza alla corrosione sono stati ricavati dal componente con geometria a scalino, che è stato prodotto mediante colata in conchiglia presso fonderia Teksid. La geometria a scalino di questo componente, caratterizzato da quattro zone distinte che presentano spessore differente, ha permesso di valutare l’effetto di differenti velocità di raffreddamento, sulle caratteristiche microstrutturali e meccaniche delleleghe in alluminio per il settore automotive. Infatti la velocità di raffreddamento aumenta muovendosi dalla zona D (zona più spessa 20 mm) alla zona A (zona più sottile 5 mm). Le proprietà meccaniche delle tre leghe sono state valutate mediante proava a flessione a tre punti (DynamometerZwick Z100), utilizzando un carico di 5KN. Dalle zone A e C sono stati ricavati campioni di dimensioni 50mmx10mmx5mm utilizzati per le prove. Mentre dalle zone B e D sono stati ricavati campioni di dimensioni standard (10mmx10mmx55mm), utilizzati per la prova Charpy. Sono stati utilizzati un pendolo strumentato da 50J e campioni non intagliati. Ricavando i campioni da differenti zone è stato possibile valutare l’effetto della velocità di raffreddamento sia sulla resistenza a flessione sia sulla resilienza delle tre leghe studiate. L’analisi microstrutturale è stata effettuata mediante l’utilizzo di un microscopio ottico (MeF4 Reichart-Jung) e di un microscopio elettronico a scansione (SEM, Leo 1450VP), equipaggiato con una microsonda EDS (Oxford microprobe), utilizzata per le analisi composizionali. I campioni sono stati preparati con tecniche standard di preparazione metallografica. L’identificazione della fase è stata condotta mediante diffrazione di Raggi-X (X-ray, PANanalytic). Infine è stata studiata, mediante una prova condotta secondo la normativa BS 11846 metodo B, la resistenza alla corrosione intergranulare di queste leghe. In questa prova inizialmente i campioni sono stati puliti mediante acetone ed etanolo, successivamente sono stati sottoposti ad un attacco alcalino (immersione per 5 min in una soluzione al 7.5% in peso di NaOH, mantenuta ad una temperatura compresa tra 55-60°C), infine sono stati immersi per 24 ore in una soluzione salina acidificata (30 g di NaCl e 10 ml di HCl per litro). Al termine della prova i campioni sono stati lavati in acqua ed etanolo ed asciugati. La suscettibilità alla corrosione intergranulare è stata valutata misurando la profondità di penetrazione della corrosione e la perdita di peso. La prova di flessione a tre punti e la prova Charpy, al fine di studiare l’effetto della corrosione sulle proprietà meccaniche e sulla resilienza, sono state effettuate anche su campioni precedentemente sottoposti alla prova di corrosione.
Risultati e analisi dell’analisi microstrutturale delle leghe d’alluminio per il settore automotive
La microstruttura delle tre leghe è costituita principalmente da grani α-Al e dalla fase eutettica Al-Si. Inoltre sono stati individuati cristalli di silicio primari ed intermetallici Mg-Si. I valori della spaziatura dendritica secondaria (SDAS), così come la forma e la dimensione del silicio eutettico, sono influenzati dalla velocità di raffreddamento, infatti aumentando la velocità di raffreddamento il valore dello SDAS diminuisce, a causa del maggior sottoraffreddamento e della maggiore velocità di movimento dell’interfaccia solido-liquido. Osservando le micrografie si può notare come all’aumentare della velocità di raffreddamento la dimensione delle particelle di silicio eutettico diminuisca e la loro morfologia diventi più fine.
La modifica del silicio eutettico, per quanto riguarda le leghe AlZn10Si8Mg1 e AlZnSi8Mg3, risulta essere influenzata non solo dalla velocità di raffreddamento ma anche dalla percentuale in peso di Mg. Infatti il Mg sembra agire da modificante per le particelle di Si quando il suo contenuto è aumentato fino al 3% in peso. Un’elevata velocità di raffreddamento rinforza l’effetto di modifica dovuto alla presenza del Mg. Nella lega AlZn10Si8Mg1 le particelle di Si appaiono più fini rispetto a quelle della lega AlZn10Si8Mg, tuttavia presentano comunque ancora una morfologia lamellare, mentre nella lega AlZn10Si8Mg3 appaiono ancora più fini e con una struttura globulare.
Al fine di poter valutare la morfologia delle particelle di silicio, alcune loro caratteristiche microstrutturali sono state misurate: l’area, la rotondità ed infine il diametro equivalente.
Si può notare come per qualunque delle quattro zone del campione a scalino considerate, aumentando il contenuto di Mg, si ottengano particelle di Si più fini. Comunque solo con una percentuale in peso di Mg del 3%, tali particelle mostrano una struttura globulare. Con una percentuale in peso di Mg pari all’1%, l’area di queste particelle diminuisce, ma presentano ancora una morfologia lamellare. A parità di contenuto di Mg, aumentando la velocità di raffreddamento, la dimensione delle particelle di silicio diminuisce. Osservando le microstrutture è possibile concludere che la modifica delle particelle di silicio eutettico più efficace, si ottiene utilizzando un’elevata velocità di raffreddamento ed un’alta percentuale in peso di Mg.
È possibile inoltre osservare l’andamento della rotondità delle particelle di silicio eutettico al variare delle velocità di raffreddamento e del contenuto di Mg. La rotondità è stata calcolata utilizzando la seguente formula:
R = p2/ 4 π A
dove p e A rappresentano rispettivamente il perimetro e l’area delle particelle di Si.
La rotondità mostra un andamento decrescente aumentando il contenuto di Mg fino al 1% in peso e solo nel caso della zona A mostra un diverso andamento. Mentre aumentando il contenuto di Mg fino al 3%, la rotondità aumenta ad eccezione del caso relativo alla zona D. Un’elevata velocità di raffreddamento ed un alto contenuto di Mg consentono di ottenere un valore di rotondità il più possibile vicino ad 1, il che corrisponde ad una particella di forma sferica.
Particelle di silicio con una morfologia sferica hanno una minore tendenza ad agire da zone di concentrazione degli sforzi e di conseguenza da possibili siti di nucleazione di cricche. La sferoidizzazione del Si può anche essere ottenuta durante la fase di solubilizzazione del trattamento termico. Per valutare la sferoidizzazione delle particelle di silicio è stato calcolato il loro diametro equivalente, utilizzando la seguente formula:
Deq= ( A / 4 π) ½
dove A corrisponde all’area delle particelle. I valori del diametro equivalente mostrano un andamento decrescente all’aumentare della velocità di raffreddamento, ovvero muovendosi dalla zona D alla zona A. Questo è dovuto dall’incremento della velocità di nucleazione e alla riduzione della velocità di diffusione. Un’elevata velocità di raffreddamento ed un alto contenuto di Mg consentono di ottenere i valori più bassi di diametro equivalente.
I segnali relativi alla matrice di α-Al e al Si sono stati individuati in ogni spettro, mentre al crescere del contenuto di Mg si può osservare un aumento dell’intensità del segnale relativo ai precipitati di rafforzamento Mg2Si. Inoltre, nei diffrattogrammi di tutte e tre le leghe sono stati identificati i picchi di diffrazione relativi ai precipitati MgZn2.
Resistenza delle leghe d’alluminio per il settore automobilistico alla corrosione intergranulare
È possibile osservare una corrosione localizzata sviluppatasi prevalentemente all’interfaccia tra le particelle di Si e la matrice di α-Al, questo perché le particelle di silicio si comportano come catodi rispetto alla matrice di alluminio.
La corrosione intergranulare è avvenuta anche all’interfaccia tra la matrice di alluminio e gli intermetallici da catodi nei confronti dell’α-Al. Tramite l’aggiunta di Mn è possibile ridurre il comportamento catodico di questi intermetallici rispetto alla matrice di alluminio.
Aumentando il conenuto di Mg fino al 3% del peso è stata osservata la precipitazione di intermetallici di Mg, che hanno agito da anodi durante il processo di corrosione. Inoltre, a seguito dell’aumento del contenuto di Mg, è aumentato il contenuto dei precipitati di rafforzamento Mg2Si, i quali si comportano da anodi rispetto alla matrice di alluminio. Quindi grazie all’aumento della frazione in volume dei precipitati Mg2Si e degli intermetallici del Mg, entrambe con comportamento anodico rispetto alla matrice in alluminio, è stato possibile aumentare la resistenza alla corrosione delle leghe autoinvecchianti in alluminio, aumentando il contenuto di Mg. Infatti la lega AlZn10Si8Mg3 presenta il più basso valore sia per quanto riguarda la perdita di peso sia per quanto concerne la profondità di penetrazione della corrosione.
Proprietà meccaniche delle leghe d’alluminio del settore automobilistico
Le proprietà meccaniche delle tre leghe autoinvecchianti sono state valutate tramite prova di flessione a tre punti e prova Charpy, sia prima sia dopo la prova di corrosione intergranulare, in modo da poter valutare l’effetto della corrosione sulla resistenza meccanica e sulla resistenza delle leghe. Nel caso delle leghe AlZn10Si8Mg e AlZn10Si8Mg1 la corrosione ha causato una diminuzione di circa il 20% del carico di rottura a flessione. La lega AlZn10SiMg3 presenta invece valori simili sia prima che dopo la prova di corrosione.
Lo stesso andamento è stato riscontrato nella deformazione a rottura.
Le leghe AlZn10Si8Mg e AlZn10Si8Mg3 hanno presentato, dopo la prova di corrosione intergranulare, una diminuzione della resilienza di circa il 25%, mentre la lega AlZn19Si8Mg1 presenta valori di resilienza confrontabili prima e dopo la prova di corrosione.
Conclusioni dello studio per l’utilizzo delle leghe d’alluminio nel settore dell’automotive
Le leghe di alluminio autoinvecchianti, grazie alla possibilità di raggiungere buone caratteristiche meccaniche senza la necessità di essere sottoposte ad un trattamento termico, rappresentano un potenziale candidato per quanto riguarda la produzione di componenti meccanici. L’utilizzo di leghe d’alluminio nel settore automobilistico consente infatti a tale industria di ottenere importanti vantaggi da un punto di vista economico e sull’impatto ambientale. Le conclusioni che possono essere tratte dai risultati ottenuto fino ad ora sono:
- Utilizzando elevate velocità di raffreddamento ed un alto contenuto in peso di Mg (3 wt%) è possibile ottenere una microstruttura caratterizzata da particelle di silicio fini e globulari. Questo consente di ridurre la probabilità, per queste particelle, di agire da siti di nucleazione preferenziale di cricche;
- Aumentando il contenuto di Mg è possibile migliorare la resistenza alla corrosione intergranulare, grazie all’aumento della frazione in volume dei precipitati Mg2Si e degli intermetallici del Mg, i quali presentano entrambi un comportamento anodico rispetto alla matrice di alluminio;
- Le leghe con un minor contenuto di Mg presentano una diminuzione della resistenza meccanica di circa il 20% dopo essere state sottoposte ad una prova di corrosione intergranulare. Le leghe ad alto contenuto di Mg invece presentano le stesse proprietà meccaniche prima e dopo la prova di corrosione;
- Percentuali in peso di Mg superiori all’1% influiscono negativamente sulla resilienza delle leghe.