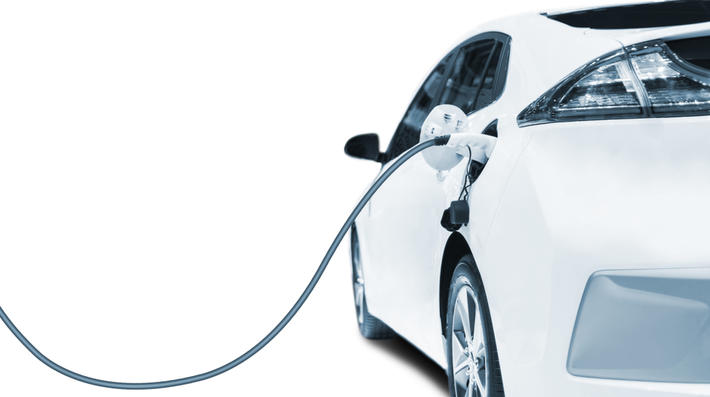
Un nuovo progetto prevede di rendere l’industria europea della produzione di veicoli elettrici meno dipendente dalle importazioni di alluminio
L’alluminio è un metallo essenziale per la produzione automobilistica elettrica dell’UE. Un nuovo progetto promette ora di mantenere questo settore pulito e a basso costo attraverso un’economia circolare. Scopriamo insieme come.
L’alluminio nella produzione dei veicoli elettrici
Nell’ultimo anno, il mercato dei veicoli elettrici ha registrato una crescita notevole, che per il momento non sembra dare segni di rallentamento. A livello globale, solo nel primo trimestre del 2022 sono state vendute due milioni di auto elettriche, il 35% in più rispetto all’anno precedente nonostante le difficoltà riscontrate sulle catene di approvvigionamento.
Il passaggio dai motori a combustione interna ai veicoli elettrici è forse una delle innovazioni di maggiore importanza nella lotta ai cambiamenti climatici. Tuttavia, le auto elettriche richiedono anche diverse materie prime e leghe specifiche di cui i veicoli a diesel e benzina non hanno bisogno.
A causa dell’attuale clima geopolitico, i legislatori europei stanno ora pianificando di riprendere le estrazioni di materie prime a livello locale entro i prossimi anni – nel caso del magnesio, già dal 2025. Tuttavia, un aumento della produzione primaria e delle estrazioni minerarie potrebbe anche causare un drastico aumento delle emissioni di CO2, sabotando il piano dell’Europa di diventare “carbon neutral” entro il 2050.
Il progetto SALEMA: la soluzione per l’alluminio nella produzione di veicoli elettrici
Una soluzione a questo problema potrebbe ora venire da SALEMA (salemaproject.eu), un progetto di ricerca finanziato dall’Unione europea. Attraverso questa iniziativa, partita nel maggio del 2021, 16 partner in sei paesi europei hanno unito le forze per rendere il settore dei veicoli elettrici più ecologico, riducendo al contempo la dipendenza dell’UE dalle importazioni di materie prime. Il progetto durerà tre anni e si svilupperà in sei diversi siti dimostrativi.
L’alluminio è fondamentale per le future auto elettriche, soprattutto per via della sua caratteristica principale: la leggerezza. Il peso della batteria è uno dei problemi principali dei veicoli elettrici moderni. Un telaio più leggero in alluminio rende questo aspetto meno critico, offrendo all’auto un’autonomia maggiore. Per questi motivi, nella produzione di veicoli elettrici, l’alluminio è diventato particolarmente importante, nonostante il suo utilizzo nelle automobili non sia una novità. Circa il 15% della carrozzeria di un’auto a combustione interna è in alluminio. Tuttavia, questa percentuale è superiore al 50% per i veicoli elettrici. Questa è tra le caratteristiche che rendono i veicoli elettrici fondamentali per il futuro dei trasporti. Nelle auto che funzionano a combustione interna tradizionale, l’alluminio è utilizzato principalmente nel motore, mentre nei veicoli elettrici è impiegato nel telaio stesso, una caratteristica che permette anche un migliore assorbimento degli urti. L’alluminio ha poi un’alta conducibilità termica, cosa che facilita la dissipazione del calore dalla batteria. In pratica, permette sia un aumento dell’autonomia dell’auto che della sicurezza del conducente.
L’alluminio è una delle risorse più versatili presenti sul mercato, al punto che il 75% di tutto l’alluminio prodotto nella storia di questa industria è ancora in circolazione, in una forma o nell’altra. Finora, tuttavia, l’alluminio riciclato è stato utilizzato principalmente per applicazioni che non richiedevano lavorazioni meccaniche.
Nuove applicazioni automotive per l’alluminio riciclato
L’alluminio è sempre stato riciclato, ma principalmente per produrre componenti di bassa qualità, come requisiti meccanici medi e getti. Ora si stanno progettando e sviluppando leghe per stampaggio, estrusione e pressocolata, che fino ad ora dovevano essere realizzate esclusivamente con alluminio primario. Questo consentirà di lavorare con applicazioni prima impossibili.
Nello specifico, SALEMA dimostrerà il potenziale di queste nuove leghe nella produzione dei veicoli elettrici utilizzando cinque casi di studio basati su diverse componenti in alluminio:
- La torre dell’ammortizzatore;
- Il telaio frontale;
- I montanti B;
- Il vano batteria;
- Il body-in-white (le parti esterne dell’auto assemblate prima della verniciatura).
Le ricerche di base per lo sviluppo di leghe parzialmente riciclateaiuterà, inoltre, i produttori di alluminio ad adattare i loro processi ai cambiamenti necessari. Ciò includerà anche le procedure di pressocolata e stampaggio. Queste leghe di nuova concezione saranno inoltre realizzate con un basso contenuto di materie prime, il che significa che utilizzeranno meno risorse. Inoltre, la già citata longevità dell’alluminio consentirà anche il riutilizzo del magnesio e del silicio.
SALEMA scommette su due soluzioni diverse per la sostituzione di questi elementi: uno è riciclare alluminio di scarto, estraendo le materie prime già presenti in esso. Il secondo metodo prevede invece la loro sostituzione con altri elementi non critici, come ferro e manganese. Esistono leghe a base di ferro con manganese che hanno eccellenti proprietà meccaniche.
Nei prossimi tre anni, le nuove leghe SALEMA saranno messe alla prova nei cinque casi di studio già citati e valutate in termini di prestazioni, con l’obiettivo di identificare i processi più promettenti per accelerarne l’adozione da parte del mercato. In caso di successo, questo modello di economia circolare applicato all’alluminio per il settore automobilistico potrebbe portare a una nuova era di produzione sostenibile. I vantaggiandrebbero potenzialmente anche al di là della sola industria dell’auto elettrica. Oltre all’aviazione, al trasporto ferroviario e all’imballaggio, un altro settore promettente è infatti quello dell’edilizia. Se utilizzato con altri materiali classici, come il vetro, l’alluminiogarantisce ulteriore stabilità, longevità e in generale una maggiore sicurezza.
Un progetto come SALEMA conferma come le nuove sfide possano portare innovazione anche in industrie all’apparenza ben consolidate. La malleabilità dell’alluminio era già nota da secoli, eppure, grazie alle conoscenze industriali moderne, sta ora accelerando lo sviluppo di nuove tecnologie a basse emissioni di carbonio, con conseguenti vantaggi sia per l’economia sia per l’ambiente.
Fonte: A&L Aluminium Alloys Pressure Diecasting Foundry Tecniques