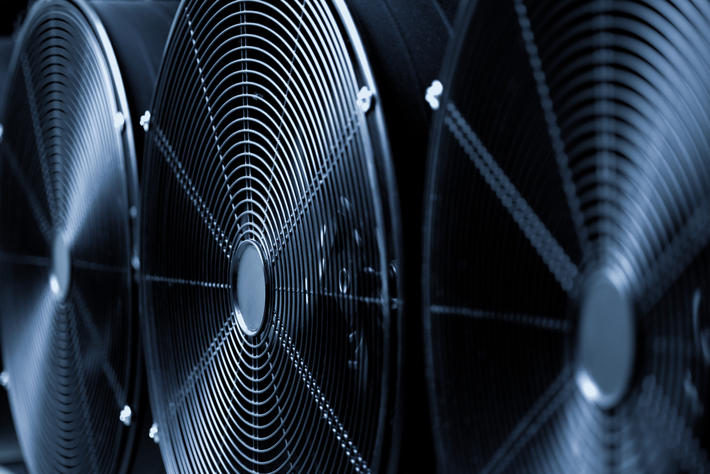
Risparmio energetico fonderie: i consumi elettrici dei ventilatori
I ventilatori industriali trovano largo impiego all’interno delle fonderie. Spesso con potenze installate medio grandi, queste macchine si ritrovano a lavorare in condizioni che ne compromettono l’efficienza.
Da oltre un anno i costi energetici sono saliti alle stelle, rendendo insostenibile la produzione per le aziende manifatturiere e in particolare per le fonderie.
Questa crisi nasconde però un’opportunità non indifferente: qualsiasi investimento che produca un efficientamento energetico si ripaga con tempi molto più rapidi.
Servono però delle azioni rapide per ridurre i consumi – e quindi i costi – energetici.
Da diversi mesi stiamo portando avanti delle attività di sensibilizzazione e divulgazione sui possibili risparmi ottenibili in poco tempo, con budget ridotti, sui consumi dei ventilatori industriali.
Perché preoccuparsi dei consumi elettrici dei ventilatori?
Queste macchine hanno generalmente un peso di circa il 14% sul totale dei costi elettrici. Una quota non enorme, ma nemmeno irrilevante. Soprattutto se si considera che molto spesso i ventilatori – per come sono acquistati o per come sono gestiti – comportano degli sprechi energetici che possono anche superare il 50% dell’energia utilizzata.
Inoltre, per tagliare i costi energetici dei ventilatori non sono necessari grossi investimenti e nella quasi totalità dei casi non si deve neppure sostituire la macchina.
È però fondamentale un’analisi accurata delle condizioni in cui devono lavorare i ventilatori e gli impianti cui sono collegati.
Nessuna azione di efficientamento energetico di un ventilatore sarà veramente efficace se non si basa su una fotografia completa del reale funzionamento dell’impianto in cui è installato e dei diversi bisogni produttivi.
È proprio in questa analisi preliminare che si possono individuare le principali aree di efficientamento e risparmio energetico.
Come scovare le condizioni tipiche di spreco energetico nei ventilatori industriali installati negli impianti
Sono state individuate delle situazioni tipiche che causano un funzionamento non efficiente dei ventilatori.
La prima fra tutte è legata alla regolazione della portata erogata dal ventilatore. In molte applicazioni, infatti, l’impianto ha bisogno di una portata di aria o di gas che varia nel tempo. Il caso più emblematico è quello dei ventilatori collegati ai bruciatori, che devono fornire una certa massa d’aria in funzione della massa di gas da bruciare. Purtroppo, è pratica comune realizzare questa regolazione in un modo errato non solo dal punto di vista energetico, ma spesso anche da quello dell’affidabilità del ventilatore stesso.
La portata erogata viene infatti gestita strozzando una valvola a valle del ventilatore. Per regolazioni entro un range ridotto della portata, questo metodo non crea problemi di tipo meccanico. Quando però sono necessarie regolazioni che arrivano a rapporti 1:10 rispetto alla portata nominale, si va incontro a un funzionamento instabile del ventilatore con forti pulsazioni della pressione in uscita (e quindi delle fiamme ai bruciatori), un rumore cupo e ciclico e guasti ai cuscinetti e/o alla struttura della macchina stessa.
Regolare con una valvola sulla mandata comporta in ogni caso un consumo elettrico molto più elevato rispetto ad altri sistemi di regolazione.
Altra situazione in cui si possono ottenere dei risparmi energetici nelle fonderie non indifferenti, è quella dei ventilatori collegati agli impianti di aspirazione e depolverazione. Essendo impianti non “produttivi” ma spesso imposti per legge, la tendenza è quella di acquistarli al minor prezzo. Ovviamente, quindi, la qualità e l’efficienza dei ventilatori installati saranno adeguate al basso costo di acquisto.
L’ideale sarebbe già in fase di acquisto dell’impianto imporre che il ventilatore industriale sia a elevato rendimento, considerato che lavorerà principalmente con fumi privi di polvere. Sfortunatamente è molto comune imbattersi in macchine che hanno rendimenti medio bassi, tra il 50% e il 60%.
Secondo le analisi, però, è possibile ottenere un risparmio dei consumi pari ad almeno un 20%, senza dover sostituire il ventilatore.
Oltre a queste due situazioni tipiche, ve ne possono essere anche altre che si possono valutare solo di volta in volta con opportune misurazioni. Va detto che in una fonderia è quasi scontato trovare dei ventilatori adibiti ai bruciatori e altri installati su impianti di depolverazione. Ha quindi quasi sempre senso procedere con la fase successiva di misurazione dei consumi e conseguente analisi degli scenari di efficientamento.
Da questa seconda fase, una volta acquisiti i parametri di funzionamento, le potenze assorbite e i vari bisogni dell’impianto in termini di produttività e flessibilità, è possibile valutare quale strategia di efficientamento energetico abbia senso adottare.
Quali strategie di efficientamento energetico è possibile utilizzare per i ventilatori?
Esistono fondamentalmente tre diverse soluzioni per ridurre i consumi elettrici dei ventilatori nelle fonderie:
1. Utilizzare una serranda di regolazione (dapò);
2. Impiegare un variatore di frequenza (inverter);
3. Installare una girante a maggior rendimento.
Le prime due possono essere utilizzate per regolare la portata del ventilatore in sostituzione delle valvole a farfalla solitamente posizionate sulla bocca di mandata. La serranda di regolazione, chiamata in gergo Dapò o IGV, permette un più ampio range di regolazione della portata. È infatti possibile operare, senza alcun problema per il ventilatore né per l’impianto, con portate che variano dal 10% al 100%.
L’inverter invece permette di ridurre la velocità di rotazione del ventilatore, diminuendo di conseguenza la portata erogata. Questa strategia di efficientamento permette un maggior risparmio energetico rispetto alla serranda dapò. Per contro però non può essere utilizzata nei casi in cui si debba ridurre la portata mantenendo un valore abbastanza simile di pressione richiesta dall’impianto (ad esempio con bruciatori rigenerativi). In queste situazioni si va incontro al fenomeno del pompaggio con instabilità delle fiamme e danneggiamenti al ventilatore stesso.
La terza strategia invece è ottimale nel caso degli aspiratori installati sugli impianti di depolverazione, che, come detto, sono solitamente scelti più in base al prezzo che non all’efficienza. Senza sostituire l’intero ventilatore, è possibile installare una girante che – a parità di portata aspirata – riesca a ridurre drasticamente la potenza assorbita.
È infine possibile avvalersi di un mix delle tre strategie viste, se questo permette una riduzione più efficace dei consumi.
Dalla teoria alla pratica: caso studio di efficientamento energetico e abbattimento dei consumi energetici su ventilatori aria comburente
Per meglio comprendere il corretto metodo da utilizzare per ridurre i consumi elettrici dei ventilatori nelle fonderie, riportiamo di seguito il caso di una consulenza applicata.
Sono stati analizzati quattro ventilatori a servizio di altrettanti bruciatori. Le potenze installate erano le seguenti:
- Ventilatore 1: 22 kW
- Ventilatore 2: 22 kW
- Ventilatore 3: 11 kW
- Ventilatore 4: 30 kW
La portata d’aria veniva regolata su ogni ventilatore mediante una valvola a farfalla posta nella tubazione a valle. I ventilatori dovevano funzionare sostanzialmente in due modalità. Per la maggior parte del tempo, la valvola a farfalla era chiusa parzialmente. In casi di emergenza invece, veniva aperta completamente per consentire il massimo afflusso d’aria.
Qualsiasi azione di efficientamento energetico doveva quindi tenere conto di queste due diverse esigenze. Ridurre la taglia dei ventilatori per evitare di parzializzare la serranda era quindi una strada non percorribile.
Ecco un esempio di come queste considerazioni, che possono nascere solo durante un’analisi preliminare dell’impianto e dei ventilatori, sono fondamentali per garantire il successo dell’azione di efficientamento energetico.
Senza valutare tutte le reali esigenze dell’impianto, sarebbe stato naturale decidere di acquistare ventilatori più piccoli – e quindi con minori consumi – così da evitare di strozzare le portate con delle serrande a farfalla, perdendo di fatto la possibilità di gestire la situazione di emergenza.
Dopo aver compreso tutti i reali bisogni d’impianto, il passo successivo è quello della misura dei valori di portata e di potenza assorbita effettiva. Una volta acquisiti questi dati, è possibile iniziare a fare delle simulazioni considerando le diverse strategie mostrate in precedenza.
In questa fase è importante conoscere molto bene i ventilatori industriali e il loro funzionamento. Il rischio è infatti quello di portare le macchine a lavorare in condizioni non sicure e instabili.
Il caso in esame si prestava a utilizzare due delle strategie viste: sostituzione delle giranti con altre a maggior rendimento e regolazione mediante variatore di frequenza (inverter). Di concerto con il cliente è stata però optata la sola installazione degli inverter, in quanto il beneficio aggiuntivo in termini di risparmio energetico dovuto alle nuove giranti era minimo rispetto all’aumento dei costi necessari all’intervento.
La potenza assorbita con inverter tiene conto delle perdite energetiche dovute all’introduzione dell’inverter e del minor rendimento con cui lavora il motore elettrico quando funziona a condizioni di carico più basse rispetto alla potenza nominale.
Secondo quanto affermato dal cliente, l’impianto funziona 7.200 h all’anno in condizioni normali.
Moltiplicando quindi le potenze risparmiate per il numero di ore annue si può avere un’idea molto più chiara dell’effettivo risparmio ottenuto, ovvero 183.600 kWh/anno.
Si può anticipare a questo punto un pensiero che potrebbe emergere in chi legge: “In qualsiasi situazione si possono ottenere dei risparmi così ingenti, pari quasi al 40% dei consumi iniziali?”.
La risposta è negativa. Non sempre si ottengono riduzioni così forti dei costi energetici dei ventilatori. A volte si possono raggiungere risparmi anche maggiori, e in altri casi invece non è economicamente conveniente un’azione di efficientamento energetico.
L’analisi preliminare che viene svolta per chi chiede di ridurre i consumi ha lo scopo di valutare se ci siano le condizioni o meno per ottenere un beneficio economico che valga l’investimento. Non è possibile garantire un risparmio energetico dei ventilatori nelle fonderie senza aver prima svolto l’analisi preliminare e la campagna di misurazioni sul campo.
Fonte: In Fonderia – ll magazine dell’industria fusoria italiana