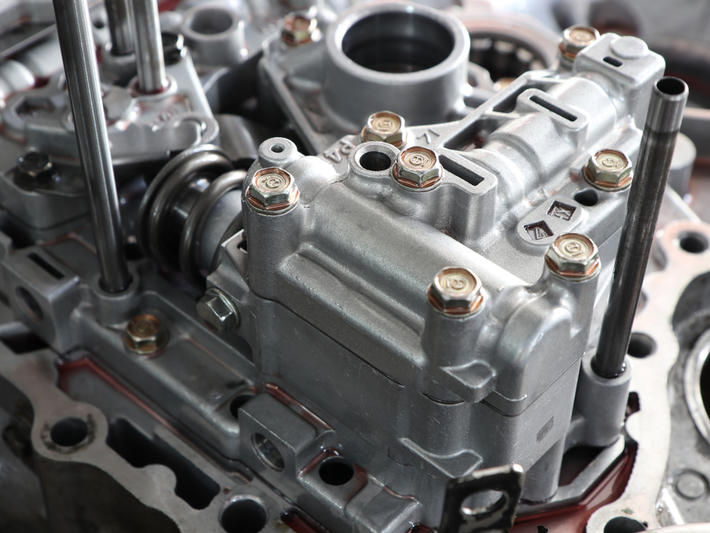
Analisi sperimentale e numerica dei difetti di fusione e da riempimento in getti colati in lega AlSi7Cu0.5Mg
Le fonderie di leghe leggere attualmente necessitano di produrre componenti di alta qualità, con geometrie complesse e brevi tempi di sviluppo, mantenendo alta la resa del processo produttivo e limitando gli scarti. Minimizzare la produzione di componenti non conformi alle specifiche comporta un doppio vantaggio:
- Un aumento della produttività, quindi del margine aziendale;
- Una riduzione dei costi legati al dispendio energetico in fase di fusione.
I software di simulazione numerica di processi di fonderia si rivelano, quindi, uno strumento essenziale per permettere alle aziende di rimanere competitive sul mercato. L’accurata previsione della formazione di difetti nei getti delle leghe leggere in fase da riempimento e di solidificazione permette l’implementazione di miglioramenti atti ad aumentare l’integrità del componente finale.
Tra i difetti di fusione che compromettono maggiormente le prestazioni di un getto si hanno i bifilms di ossido. Tali difetti, generati durante le fasi di preparazione del metallo, di versamento e di riempimento, fungono da promotori per la formazione di porosità da ritiro, porosità gassose e strappi a caldo. Un componente privo di bifilms risulterebbe integro, privo anche di qualsiasi difetto generato durante al solidificazione del materiale.
Lo sviluppo di un software di simulazione numerica in grado di prevedere accuratamente la formazione di difetti nei getti delle leghe leggere da riempimento faciliterebbe l’implementazione di miglioramenti di processo e di design di prodotto, atti a ridurre gli scarti e ad aumentare il margine aziendale.
Tale studio mira a valutare l’affidabilità dei modelli numerici di previsione della formazione di difetti da fusione e da riempimento implementati in FLOW-3D Cast, un software commerciale di simulazione numerica di processi di fonderia. Tale valutazione è eseguita tramite comparazione con dati sperimentali.
Un’analisi numerica preliminare ha permesso di individuare i parametri di processo che favoriscono la formazione di difetti da fusione e da riempimento. Per il processo di colata si è scelta una lega AlSi7Cu0.5Mg (EN AC-45500) e due geometrie di stampi:
- lo stampo per la realizzazione di provini colati a parte a sezione circolare;
- lo stampo per la produzione di provini colati a parte a sezione rettangolare.
L’analisi degli output numerici della frazione di volume di aria intrappolata e della concentrazione di difetti generata sulla superficie a contatto con l’atmosfera ha permesso di individuare le condizioni di colata più critiche, riprodotte poi sperimentalmente.
Per promuovere il quantitativo finale di difetti da fusione, tutti i getti sono stati colati senza il filtro. Si è verificata la ripetibilità delle prove sperimentali monitorando la variazione delle temperature durante il processo di colata e filmando la fase di riempimento degli stampi. Inoltre, i dati raccolti durante la campagna sperimentale hanno permesso l’implementazione numerica di processo tramite operazioni di Reverse Engineering.
I getti colati sono stati successivamente caratterizzati dal punto di vista microstrutturale. Analizzata la composizione chimica della lega, si è misurata la spaziatura tra i rami interdentritici secondari (SDAS) e si è mappata la distribuzione dei difetti generati dalla presenza di bifilms di ossido.
Dall’analisi dei risultati ottenuti, si evince che il software modella accuratamente il comportamento fluidodinamico del metallo; si ha infatti corrispondenza tra la simulazione del riempimento dello stampo e i video registrati durante la campagna sperimentale. Si è inoltre verificata la coerenza tra i tempi di solidificazione simulati e le tempistiche sperimentali.
L’accuratezza con cui il software prevede l’intrappolamento di bifilms di ossido è stata valutata confrontando la mappatura difettologica sperimentale e gli output numerici dell’aria intrappolata e della generazione di difetti nei getti delle leghe leggere. Nello stampo per provini a sezione rettangolare si ha buona corrispondenza tra dati numerici e sperimentali: alte densità di difetti sono individuabili nella parte centrale superiore del filtro e nel tratto utile.
Al contrario, nel getto a sezione circolare sono individuabili delle divergenze tra risultati numerici e sperimentali. Nella simulazione, le aree adiacenti alle superfici a contatto con l’atmosfera mostrano una concentrazione di difetti nei getti delle leghe leggere molto più alta di quella rilevata sperimentalmente. Inoltre, i difetti si concentrano principalmente nella zona a valle del filtro, area che nella realtà risulta pressoché integra. Tali divergenze sono legate al modello eccessivamente semplificativo utilizzato per prevedere la formazione di difetti da fusione e riempimento.
Si può quindi concludere che è verificata l’affidabilità del software nel modellare il comportamento fluidodinamico del metallo e nel prevedere la formazione di difetti nei getti delle leghe leggere nelle zone interne del getto. Alcuni miglioramenti al codice di calcolo si rivelano invece necessari per prevedere la distribuzione di difetti di fusione nelle aree adiacenti a superfici a contatto con l’atmosfera.
Fonte: In Fonderia – Il magazine dell’industria fusoria italiana, n. 2 – 2021